Insert Molding Service

What is Insert Moulding?
Insert molding services is an injection molding process .The process makes use of engineering plastics for improved wear resistance, tensile strength and weight reduction as well as using metallic materials for strength and conductivity. Inserts molding facilitates the manufacturing of strong, durable, and lightweight parts, which is why several industries are adopting this process.
Common inserts include pins, blades, threaded nuts and knobs, sleeves, bushings, and the metal shanks of tools, such as screwdrivers. Inserts are widely used in many moulding processes:Injection Moulding, Compression Moulding…
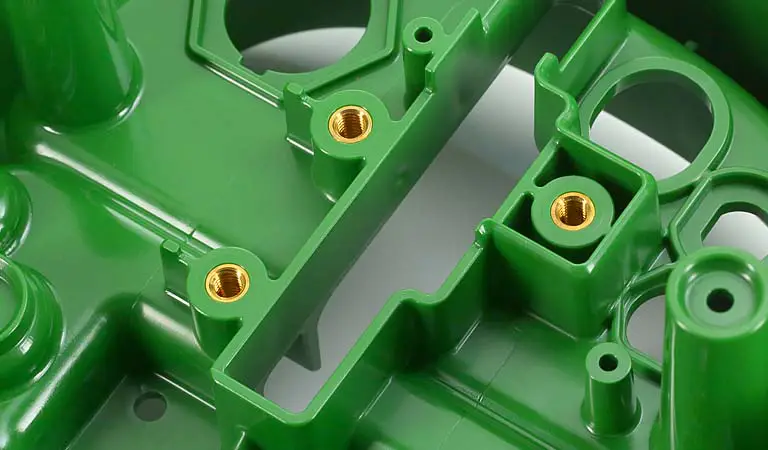
Insert Moulding Working Process
Considerations Before Insert Molding
Thinking through the following important factors well before insert molding can help you save time and money, especially for a reputable company like Flexiparts Plastic, which will tell you the specific techniques to be used and the components to be assembled into a single part.
- Insert Material Type
Insert type is the first factor to consider before insert molding. Whichever insert you decide to use, it should be able to withstand the extreme temperatures and pressures often encountered in the process. - Insert Location
The location of the insert determines the forces that will act on it over time. Any change in the position or location of the insert can disrupt the entire process, which is why steps must be taken to secure it in place. - Reducing the gap between inserts in metal parts
The gap between the metal insert molding and the molten material is a very important factor. Narrowing the gap between metal inserts improves the reliability of molding composite products. - Selection of appropriate resin and molding conditions
Choosing the right resin and molding conditions is conducive to the perfect molding of inserts. This choice is even more important when dealing with products that are easily damaged, such as electrical parts and coils. - Choosing the right mold
The molds used in insert molding not only shape the molten material, but also help hold the insert in place during the insert molding process. - Costs
Costs include the cost of the insert and the cost of hiring an operator. Another element of cost is understanding the unit price increase that will result from adding inserts. - Production Volume
Whether you use manual or automatic loading depends on production volume. Therefore, choosing the right loading method requires a cost-benefit analysis and an understanding of production requirements.
Compare Automated Insertion to Insertion by Hand
Compare | Automated Insertion | Insertion by Hand |
---|---|---|
Flexibility | Low, suitable for standardized products | High, adaptable to various shapes and sizes |
Efficiency | Higher, consistent and fast production | Lower, dependent on worker skill |
Quality Control | High consistency, easier quality monitoring | worker's experience, may be inconsistent |
Learning Curve | Longer, requires operator training | Short, easy to learn |
Productivity | Large-scale or standardized production | Small batch or custom production |
Cost | Higher equipment investment | Lower equipment investment |
Custom Plastic Parts
Custom Rubber Parts
Custom PU Parts
How Insert Molding Works?
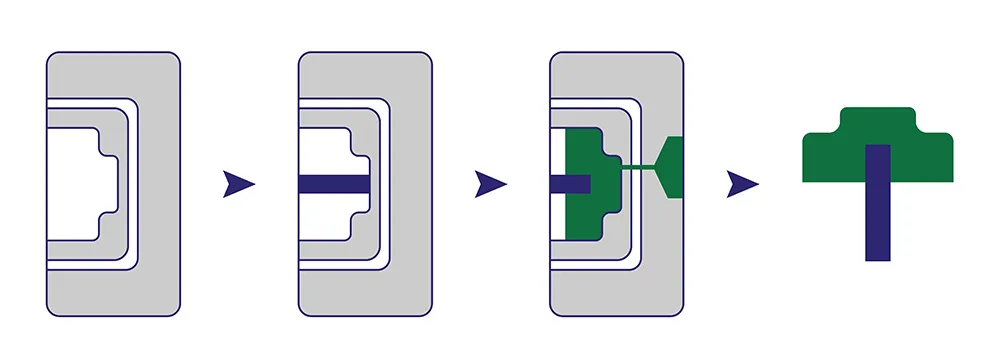
Insert molding is a multi-stage process that seamlessly combines different materials to create intricate and efficient parts. The insert moulding process involves several key steps:
- Preparation: The insert molding process begins with meticulous preparation, including selecting the right inserts and ensuring they are clean and properly arranged for placement.
- Load Inserts into the Mold: After preparation, inserts are loaded into the mold. These inserts can vary in material, shape, and purpose, depending on the final product requirements.
- Molding Inserts with Molten Plastic and Cooling: During this stage, molten plastic is injected to mold around the inserts, and the resulting part cools, ensuring a strong bond between the plastic and the inserts.
- Ejection of Moulded Parts: Once the molded part has sufficiently cooled and solidified, it is ejected from the mold. The precision of this step is crucial to avoid damage to the part.
- Quality Inspection with Finished Parts: After ejection, each part undergoes a thorough quality inspection to ensure it meets design specifications and quality standards.
Related Resources
Our Available Material
Materials for Insert Molding
Our capabilities extend to a wide range of metal inserts moulding and diverse plastic materials for plastic insert molding, providing flexible insert moulding solutions for various applications.
Types of Inserts
female threads
male threads
dowel pins
electrical contacts
spring-loaded clips
Available Plastic Molding Material
Acrylonitrile Butadiene Styrene (ABS)
Polypropylene (PP)
Polycarbonate (PC)
Polyamide (Nylon)
Polyvinyl Chloride (PVC)
Polystyrene (PS)
Thermoplastic Elastomer (TPE)
Thermoplastic Polyurethane (TPU)
Available Rubber Molding Material
Natural Rubber (NR)
Ethylene Propylene Diene Monomer (EPDM)
Fluoroelastomer (FKM)
Silicone Rubber
Styrene-Butadiene Rubber (SBR)
Nitrile Rubber (NBR)
LET’S START A NEW INJECTION MOLDED PARTS
Examples of Insert Molding Parts
- Electronic Device Housings: Many electronic devices have inserts for screws and fasteners, ensuring the components are securely held in place.
- Plumbing Fixtures: Faucet handles and showerheads may use insert molding to combine plastic and metal parts for durability and aesthetics.
- Industrial Tools: Handles of tools like screwdrivers and wrenches may have inserts for added strength and grip.
- Electrical Connectors: Insert moulding combines metal pins or sockets with sturdy plastic housings, ensuring reliable electrical connections.
Advantages of Insert Molding
Enhanced Structural Integrity
Insert moulded reinforces the bond between components, resulting in more robust and durable parts.
Reduced Assembly Costs
By integrating multiple parts into one, insert moulding reduces the need for additional assembly steps.
Improved Electrical and Thermal Performance
Inserts molding enhances conductivity and insulation properties, ideal for electrical components.
Enhanced Aesthetics
Achieve sleek and polished product finishes with precise insert molding.
What is Downside to Insert Molding?
Complex Design and Tooling
The process may require intricate tooling and mold designs, increasing initial setup costs.
Potential Insert Shift
Ensuring precise insert placement can be challenging, leading to potential misalignment issues.
Longer Cycle Times
The added step of placing inserts can extend production cycle times compared to standard molding.
Limited for Small Components
Extremely small inserts may be challenging to accommodate in the molding process.
Compare | Insert Molding | Overmolding |
---|---|---|
Process | Inserts places in mold, mateiral injected around them | Second material injected to encase preformed part |
Material Combination | Combines different materials with a part | Adds an outer layer to an existing part |
Applications | Embedding components, combing materials | Enhancing aesthetics, functionality, for ergonaomics |
Cost | Cost-effective for material combination | Cost-effective for adding outer layer or features |
Insert Molded Products We Made
At our facility, we specialize in custom plastic insert molding, delivering precision-engineered components that meet the toughest application demands. As a trusted insert molding supplier, we produce a wide range of insert molded products, from metal insert molding parts to complex assemblies like insert molding magnets. Whether you're seeking high-volume production or custom insert molding solutions, our team ensures consistent quality and performance.






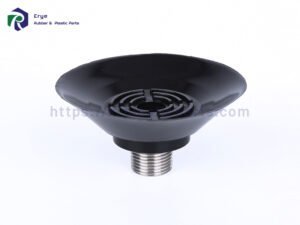