Automotive injection molding is the backbone of modern vehicle manufacturing, enabling the mass production of precise, durable, and cost-effective components. From interior trims and dashboards to exterior bumpers and under-the-hood parts, this advanced process ensures high efficiency and consistency in producing automotive plastic components. By leveraging cutting-edge materials like thermoplastics and composites, manufacturers achieve lightweight, high-strength solutions that enhance vehicle performance and sustainability. As the industry evolves, innovations in mold design, process optimization, and material selection continue to shape the future of automotive injection, driving advancements in both aesthetics and functionality.
Key Advantages of Automotive Injection Molding
Efficient High Production
Injection molding allows for fast cycle times, making it ideal for high-volume production. This efficiency is crucial in meeting the automotive industry’s demand for consistent and reliable parts.
Cost-Effectiveness
The process offers lower material costs compared to metals and reduces labor expenses. Although the initial mold creation can be costly, the cost per part decreases significantly with large production volumes.
Durability and Resistance
Injection-molded parts are highly durable and resistant to corrosion, maintaining their shape and integrity over time. This is particularly beneficial in harsh automotive environments.
Design Flexibility
Injection molding allows for complex geometries and intricate designs, enabling the creation of innovative automotive components. This flexibility supports modern vehicle designs and simplifies assembly processes.
Lightweight Components
Plastic parts are significantly lighter than their metal counterparts, contributing to improved fuel efficiency and vehicle performance. Overmoulding techniques can further reduce part weight.
Aesthetic Benefits
The process allows for the addition of colorants and surface textures directly during molding, eliminating the need for additional painting or finishing steps. This enhances cost savings and efficiency.
Material Versatility
A wide range of thermoplastic and thermosetting polymers can be used, offering flexibility in material selection to meet specific mechanical and thermal requirements.
Repeatability and Consistency
Injection molding ensures that each part produced is virtually identical, maintaining high consistency across large production runs. This repeatability is crucial for vehicle performance and safety.
Common Applications of Injection Molding in the Automotive Industry
Interior Components
Automotive injection molding is widely used for crafting interior parts such as dashboards, door panels, center consoles, and trims. These components require precision, durability, and aesthetic appeal, making plastic injection molding automotive parts an ideal solution.

Exterior Parts
Bumpers, grilles, fenders, and lighting housings are produced using automotive plastic injection molding. The process ensures impact resistance, weather durability, and seamless integration with vehicle designs.
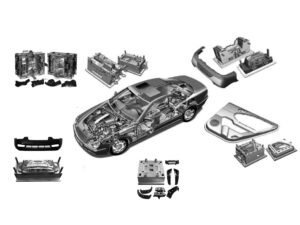
Under-the-Hood Applications
Injection molding automotive parts extend to engine covers, air intake systems, battery housings, and fluid reservoirs. These components must withstand extreme temperatures, mechanical stress, and chemical exposure while maintaining lightweight efficiency.
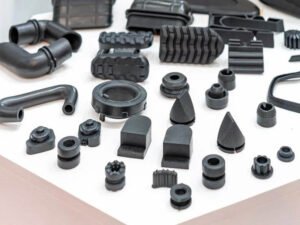
Materials Used in Automotive Injection Molding
Thermoplastics
Commonly used thermoplastics include:
- ABS (Acrylonitrile Butadiene Styrene): Provides strength and impact resistance.
- Polycarbonate: Used in lighting housings for its transparency and toughness.
- Polypropylene (PP): Lightweight and chemically resistant, ideal for fluid reservoirs and trim panels.
- Nylon: Offers excellent mechanical strength and heat resistance, making it suitable for under-the-hood applications.
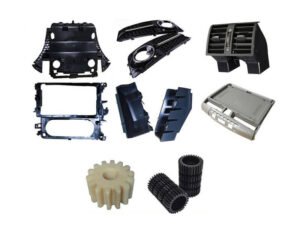
Thermosets and Advanced Composites
- Epoxy and Phenolic Resins: Used for heat-resistant applications.
- Fiber-Reinforced Plastics (FRP): Enhance strength while keeping components lightweight.
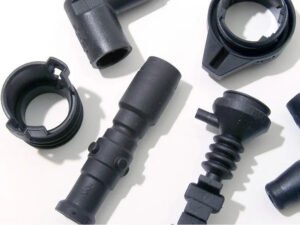
Considerations for Lightweighting and Sustainability
Automotive injection molding companies are increasingly adopting bio-based polymers and recycled plastics to reduce environmental impact. Lightweight materials improve fuel efficiency and support electric vehicle (EV) innovation.
Manufacturing Process for Auto Injection Molding
The manufacturing process for automotive injection molding involves several key steps:
Material Preparation: Selected materials, typically thermoplastic pellets, are fed into a hopper and heated in a barrel until they melt into a uniform liquid.
Injection: The molten plastic is injected into a mold cavity under high pressure using an injection molding machine. The mold is usually made from hard steel or aluminum.
Cooling and Solidification: Once the mold is filled, the material cools and solidifies. Cooling is controlled to prevent defects like warping or shrinkage.
Ejection and Finishing: After solidification, the mold opens, and the part is ejected. Any excess material is removed, and the part may undergo secondary processes like painting or assembly.
Design Considerations for Automotive Part Molding
Designing parts for automotive injection molding requires careful consideration of several factors to ensure quality and functionality:
Choosing the Right Material for Performance & Longevity
Automotive plastics must endure years of temperature fluctuations, UV exposure, and contact with fuels or lubricants. High-performance thermoplastics like PA6, PBT, and PC-ABS are common for under-the-hood components, while elastomers such as TPV and silicone provide flexibility for seals and gaskets. To reduce weight without compromising strength, manufacturers often opt for glass fiber-reinforced composites, especially in electric vehicle applications.
Optimizing Structural Integrity for Stress & Impact Resistance
Achieving the right balance between strength, flexibility, and weight reduction is critical.
- Wall thickness consistency prevents internal stress and defects like warping. A general guideline is 2-4mm, but variations depend on the part’s function.
- Rib design enhances strength without excessive material use. Engineers typically maintain a height-to-thickness ratio under 3:1 for optimal load distribution.
- Draft angles facilitate ejection from the mold and prevent surface defects. A minimum of 0.5°-3° is recommended for most automotive components.
Precision & Fit: Why Tight Tolerances Matter in Assembly
Unlike general plastic products, automotive parts must fit seamlessly with other vehicle components.
- Snap-fit housings, connector shells, and dashboard assemblies require precise tolerances, often within ±0.05mm, to ensure seamless assembly.
- Thermal expansion adjustments are crucial—plastics expand and contract based on temperature shifts, so engineers incorporate design allowances to prevent stress fractures over time.
Manufacturing Efficiency & Moldability Considerations
Efficient molding processes reduce defects and speed up production.
- Gating & flow control: Proper hot or cold runner selection ensures balanced filling, reducing weld lines and air entrapment.
- Venting & cooling: Efficient mold cooling systems (e.g., conformal cooling) minimize cycle times and prevent part deformation.
- Cycle time optimization: Automotive parts are mass-produced, so optimizing cooling rates and ejection efficiency improves throughput without sacrificing quality.
Surface Aesthetics & Secondary Finishing
For visible parts like dashboards and trim panels, maintaining Class A surface finishes is crucial.
- Mold textures & coatings help achieve a premium look without requiring post-processing.
- Paintability & adhesion considerations ensure compatibility with secondary treatments like soft-touch coatings or chrome plating.
By integrating these design principles, manufacturers can produce reliable, high-quality automotive components that meet performance expectations while staying cost-effective.
Challenges in Automotive Injection Molding
Dealing with High-Temperature Materials and Complex Geometries
Automotive injection molding often involves processing high-performance thermoplastics and composites that must withstand extreme temperatures and mechanical stress. Materials like polyamides, polycarbonates, and fiber-reinforced plastics require precise temperature control during molding to prevent warping, shrinkage, or degradation. Additionally, modern vehicle designs demand intricate geometries and thin-walled structures, making mold design and flow dynamics critical factors in ensuring defect-free parts.
Meeting Industry Regulations and Quality Standards
The automotive sector enforces strict regulatory requirements for safety, durability, and environmental impact. Injection-molded components must comply with standards such as ISO/TS 16949, ensuring consistency in quality across mass production. Manufacturers must also address rigorous crashworthiness, flame resistance, and VOC emission standards, particularly for interior components. To meet these stringent demands, advanced testing, real-time monitoring, and precision molding techniques are essential in achieving flawless automotive plastic injection molding results.
Conclusion: Why Automotive Injection Molding Matters
Automotive injection molding plays a pivotal role in modern vehicle manufacturing. Its ability to produce complex, durable, and lightweight components efficiently has revolutionized the industry. As materials and technologies continue to advance, the importance of injection molding in achieving sustainability and performance goals in automotive manufacturing will only grow.