Advantages of injeciton moulding make it is widely used manufacturing process that allows for the efficient production of complex plastic parts. This technique involves injecting molten material into a mold, where it cools and solidifies to form the desired shape. The versatility of injection molding makes it a popular choice across various industries, including automotive, consumer goods, medical devices, and electronics. With its ability to produce high-quality parts at a rapid pace, injection molding offers significant advantages over traditional manufacturing methods. In this post, we will delve into the 12 key advantages of injection molding, providing insights into why this process is often the preferred choice for mass production. Additionally, we will touch on the injection molding advantages and disadvantages, ensuring a well-rounded perspective on this essential manufacturing technique.
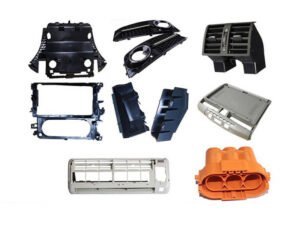
1. Fast Production and High Efficiency
One of the most significant benefits of injection moulding is its rapid production capability. The injection molding process can achieve cycle times ranging from as little as 10 seconds to about 120 seconds. This remarkable speed allows manufacturers to produce large quantities of parts in a fraction of the time required by traditional manufacturing methods.
2. Low Labor Costs
The automation involved in the injection molding process minimizes the need for manual labor, allowing manufacturers to operate more efficiently. Advanced machinery and robotics can handle various tasks, such as loading materials, operating the injection molding machine, and even performing quality checks. With automation, one operator can effectively manage multiple machines simultaneously, which drastically reduces the number of workers needed on the production floor. This streamlined approach not only lowers labor costs but also enhances productivity.
3. Design Flexibility
One of the standout benefits of moulding is its remarkable design flexibility, which allows manufacturers to create complex shapes and intricate designs that may be challenging or impossible to achieve with other manufacturing processes. The high pressure used during the injection molding process enables the molten material to fill every detail of the mold, resulting in precise and detailed parts.
4. High Production Output
A significant advantages to injection moulding is its ability to achieve high production output. Once the molds are created and set up, manufacturers can produce thousands—often millions—of identical parts before any maintenance is needed on the tooling.
5. Large Material Choice
One of the notable injection molding advantages is the extensive variety of polymer resins available for use in the manufacturing process. This diversity allows manufacturers to select materials that best suit their specific application needs, enhancing both functionality and performance. Commonly used resins include:
- Polypropylene (PP)
- Polycarbonate (PC)
- Acrylonitrile Butadiene Styrene (ABS)
6. Low Scrap Rates
One of the significant benefits of injection molding is its ability to generate minimal waste compared to traditional manufacturing methods. The only waste typically generated comes from sprues, runners, and defective parts, which represent a small fraction of the total material used. Another crucial aspect of minimizing waste in injection molding is the ability to recycle unused materials.
7. Consistent Quality and Precision
The injection molding process is known for its repeatability, that makes injection molding to deliver consistent quality and precision across all produced parts.
8. Ability to Include Inserts
One of the unique injection molding benefits is the ability to incorporate metal or plastic inserts directly into molded parts during the manufacturing process. This technique, known as insert molding, allows manufacturers to create a single, cohesive component that combines the advantages of both materials.
9. Good Color Control
Another significant advantage of injection molding is the ability to achieve excellent color control in the final products. Manufacturers can produce parts in virtually any color using techniques such as masterbatching or compounding.
Masterbatching involves creating a concentrated mixture of pigments and additives within a carrier resin, which is then mixed with the base polymer before injection. This method ensures uniform color distribution throughout the molded part, resulting in consistent and vibrant colors across large production runs.
10. Cost-Effectiveness for Mass Production
Injection molding is renowned for its cost-effectiveness, particularly in mass production scenarios. As manufacturers scale up their production runs, the fixed costs associated with mold creation are distributed over a larger number of parts. This leads to a decrease in cost per unit, making injection molding an economical choice for producing large quantities of identical items.
11. Shortened Product Development Timeline
The injection molding process also contributes to a shortened product development timeline. Advanced computer-aided design (CAD) software allows for rapid prototyping and testing of new designs before committing to full-scale production. This iterative approach helps identify potential issues early in the development process, reducing delays associated with traditional manufacturing methods.
12. Lightweight Parts
Another significant advantage of injection molding is the ability to produce lightweight parts without compromising strength or durability. Injection molding allows manufacturers to design parts that are optimized for weight reduction through the use of advanced materials and innovative design techniques. For example, hollow sections can be created within molded parts, or intricate geometries can be employed to minimize material usage while maintaining structural integrity. This characteristic is particularly beneficial in industries such as automotive, aerospace, and consumer goods, where reducing weight can lead to improved performance, fuel efficiency, and overall product effectiveness.